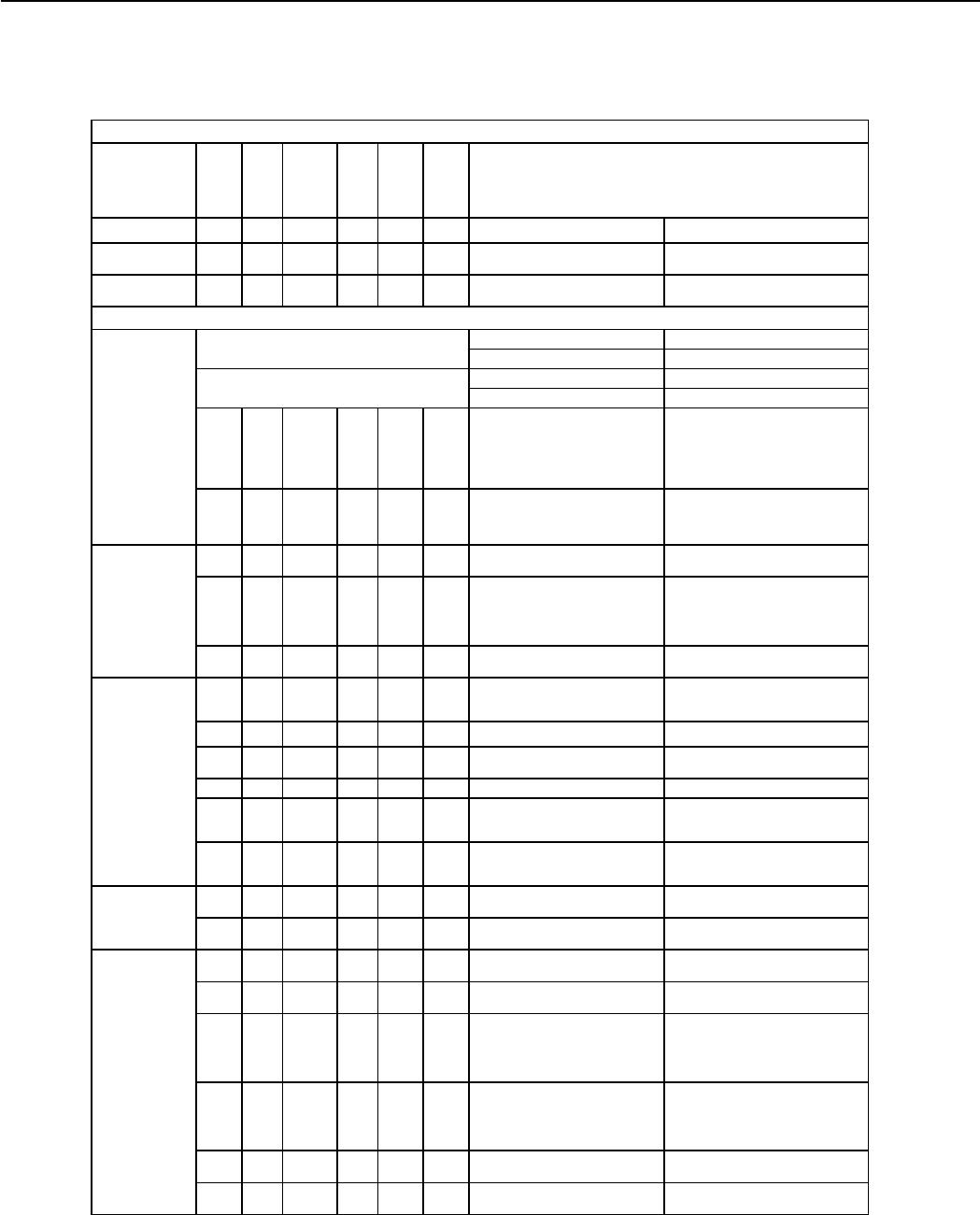
47 PB
COMPONENT TESTING
Touch Test Chart : To Service Reversing Valves
DISCHARGE TUBE
from Compressor
Tube to INSIDE
T
ube to INSIDE
Capillary Tube
RIGHT Pilot
Capillary Tube
Capillary Tube
LEFT Pilot
SUCTION
to Compressor
TUBE to
Compressor
Capillary Tube
COIL
14
COIL
NORMAL FUNCTION OF VALVE
VALVE
OPERATING
from Compressor
DISCHARGE TUBE
SUCTION TUBE
Tube to Indoor
COIL
Tube to OUTSIDE
LEFT Pilot
RIGHT Pilot
CONDITION
NOTES:
1 2 3 4 6 5 POSSIBLE CAUSES
* TEMPERATURE OF VALVE BODY
** WARMER THAN VALVE BODY
Hot
Normal Cooling
CORRECTIONS
Cool
Cool
as (2)
Hot
as (1)
*TVB TVB
Normal Heating
Hot Cool
Hot
as (1)
Cool
as (2)
*TVB TVB
MALFUNCTION OF VALVE
Valve will not
to heat.
shift from cool
Check Electrical circuit and coil
Repair electrical circuit. No voltage to coil.
Replace coil. Defective coil.
Check refrigeration charge
Repair leak, recharge system. Low charge.
Pressure differential too high. Recheck system.
Hot Cool
Cool,
as (2)
Hot,
as (1)
Hot *TVB Pilot valve okay. Dirt in one bleeder hole.
Piston cup leak
Deenergize solenoid, raise head pressure,
reenergize solenoid to break dirt loose.
If unsuccessful, remove valve, wash
out. Check on air before installing. If no
movement, replace valve, add strainer to
discharge tube, mount valve horizontally.
Valve will not
Stop unit. After pressures equalize, restart
with solenoid energized. If valve shifts,
reattempt with compressor running. If still
no shift, replace valve.
shift from cool
to heat.
Hot Cool
Cool,
as (2)
Hot,
as (1)
*TVB *TVB Clogged pilot tubes.
Raise head pressure, operate solenoid to
free. If still no shift, replace valve.
Hot Cool
Cool,
as (2)
Hot,
as (1)
Hot Hot
Both ports of pilot open. (Back seat port
did not close).
Cool Warm
Raise head pressure, operate solenoid
to free
partially clogged port. If still no shift,
replace valve.
Cool,
as (2)
Hot,
as (1)
*TVB Warm Defective Compressor. Replace compressor
Starts to shift
complete
reversal.
but does not
Hot Warm Warm Hot Hot *TVB
Check unit for correct operating pressures
and charge. Raise head pressure. If no
shift, use valve with smaller port.
Not enough pressure differential at start
of stroke or not enough fl
ow to maintain
pressure differential.
Replace valve Body damage.
Hot Warm Warm Hot Hot Hot Both ports of pilot open.
Raise head pressure, operate solenoid. If
no shift, use valve with smaller ports.
Replace valve Body damage. Hot *TVB Hot Hot Hot Hot
Hot Hot
Raise head pressure, operate solenoid. If
no shift, use valve with smaller ports.
Hot Hot
Valve hung up at mid-stroke. Pumping
volume of compressor not suffi cient to
maintain reversal.
Hot Hot Both ports of pilot open.
Apparent
Raise head pressure, operate solenoid.
If no
shift, replace valve.
leap in heat-
ing.
Hot Cool
Hot,
as (1)
Cool,
as (2)
*TVB *TVB Piston needle on end of slide leaking.
Hot Cool
Operate valve several times, then recheck.
If excessive leak, replace valve.
Hot,
as (1)
Cool,
as (2)
**WVB **WVB Pilot needle and piston needle leaking.
Operate valve several times, then recheck.
If excessive leak, replace valve.
Will not shift
cool.
from heat to
Hot Cool
Hot,
as (1)
Cool,
as (2)
*TVB *TVB Pressure differential too high.
Clogged pilot tube.
Stop unit. Will reverse during equalization
period. Recheck system
Hot
Raise head pressure, operate solenoid to
free dirt. If still no shift, replace valve.
Cool
Hot,
as (1)
Cool,
as (2)
Hot *TVB Dirt in bleeder hole.
Hot Cool
Hot,
as (1)
Cool,
as (2)
Hot
Raise head pressure, operate solenoid.
Remove valve and wash out. Check on air
before reinstalling, if no movement, replace
valve. Add strainer to discharge tube.
Mount valve horizontally.
Piston cup leak. *TVB
Hot Cool
Hot,
as (1)
Stop unit. After pressures equalize, restart
with solenoid deenergized. If valve shifts,
reattempt with compressor running. If it
still will not reverse while running, replace
the valve.
Cool,
as (2)
Replace valve. Defective pilot. Hot Hot
Warm Cool
Warm,
as (1)
Cool,
as (2)
Warm *TVB Defective compressor. Replace compressor
Figure 704 (Touch Test Chart)